Verbundholz mit homogener Masse oder koextrudiert
Verbundholz mit homogener Masse oder koextrudiert
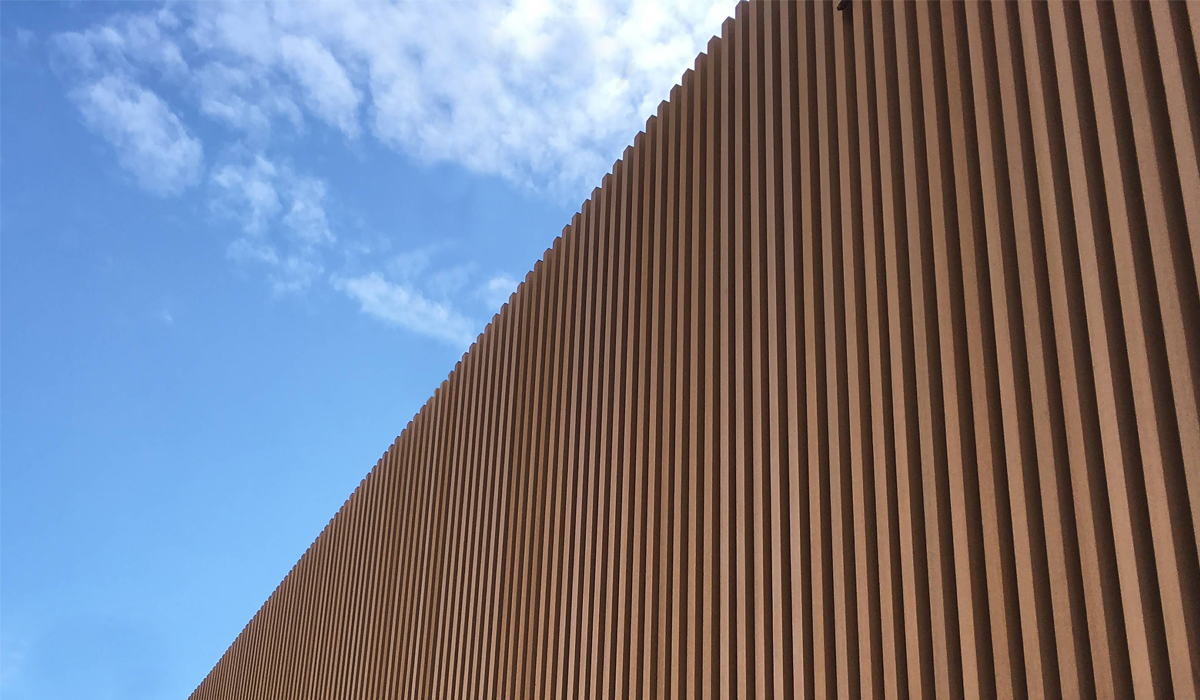
Das Verbundholz wurde in den frühen 2000er Jahren als Ersatz für Holz entwickelt. Aus diesem Grund wurde es als homogene Masse gedacht, die dem Aussehen von Holz sehr ähnlich ist: dies bedeutet, dass das Produkt vollständig aus einem einzigen, zuvor vermengten Verbundmaterial besteht.
Das aus homogener Masse hergestellte Produkt besitzt wichtige Eigenschaften, dank der Komponenten aus denen seine Formel besteht. Die 3 Hauptkomponenten sind Holz, Polymere und Zusatzstoffe, vereint in einer einzigen homogenen Masse durch ein einphasiges Extrusionsverfahren. Für alle Verbundhölzer gilt die Regel: je höher die Qualität der Hauptbestandteile ist, desto besser wird die Langlebigkeit des Produkts sein. Die Komponenten müssen in einem sehr präzisen Verhältnis vermengt und mit einem ausreichendem Druck extrudiert werden, um ein Produkt mit hoher Langlebigkeit zu erlangen.
Für weitere Informationen zum Verbundholz besuchen Sie unseren BLOG Was versteht man unter Verbundholz Infolge der steigenden Nachfrage, die vor allem vom amerikanischen und europäischen Markt ausgeht, aufgrund des zunehmenden Wettbewerbs zwischen konkurrierenden Produkten und um alternative Lösungen zu homogenem Verbundholz zu finden, haben einige Hersteller begonnen, nach Lösungen zu suchen, die die Kosten für die drei Makrokomponenten (Holz, Polymer und Zusatzstoffe) senken könnten. Das Ergebnis war ein Produkt, das in der Lage ist, das Innere des Materials (den so genannten "core") mit einem plastischen Schutzfilm mit einer Dicke von einigen hundertstel Millimetern bis zu einigen Zehnteln (normalerweise 0,05 bis 0,6 mm) zu verkleiden. Damit soll die Menge der in den "core" eingebrachten Zusatzstoffe (die im Falle von homogener Masse fast 50 % des Endprodukts ausmachen können) durch einen Film reduziert werden, der denselben gegen Angriffe durch äußere Witterungseinflüsse (Sauerstoff, Feuchtigkeit und UV-Strahlen) "versiegeln" soll.
Dieser Prozess wird mittels eines zweiten Extruders unterhalb der Matrize des Hauptextruders durchgeführt, der während der Extrusionphase eine sehr flüssige Mischung aus hauptsächlich Polymeren injiziert, die das schon teilweise ausgehärtete Innenmaterial (core) umhüllt. Der Prozess ist sehr komplex, die Mischungen und die Schmelztemperaturen zwischen den beiden Verbindungen sind entscheidend dafür, dass sich das Produkt nicht mit der Zeit wieder trennt. Das so produzierte Profil nimmt die Bezeichnung koextrudiertes Verbundholz oder Verbundholz der zweiten Generation an, gerade weil es zu einem späteren Zeitpunkt entwickelt wurde, aber das soll nicht heißen, dass diese Entwicklung positiv oder besser ist als die erste homogene Masse, es wird nur ein anderes Produkt extrudiert. Im Folgenden sehen wir, welche Vor- und Nachteile und Eigenschaften die zwei Produktkategorien unterscheiden.
Die Eigenschaften:
Die ästhetischen Eigenschaften:
Das Verbundholz mit homogener Masse fühlt sich warm an, die freiliegenden Holzfasern vermitteln die unmittelbare Anlehnung an natürliches Holz. Es besitzt ein gleichmäßiges Aussehen und wenn es von hoher Qualität ist, kann man den Duft von Holz wahrnehmen. Die ästhetischen Eigenschaften des Produkts mit homogener Masse werden auch bei koextrudierten Produkten angestrebt, indem Muster und Schattierungen auf der Oberfläche der Kunststofffolie erzeugt werden. Das Produkt fühlt sich in diesem Fall kalt an und besitzt eine glänzendere Oberfläche. Um den künstlichen Effekt zu reduzieren schleifen einige Hersteller die Oberfläche, doch reduziert sich so die Dicke des Films und es bilden sich unansehnliche Plastikfäden.
Die Schnitte und Verarbeitungen auf Verbundholz:
Die Bearbeitung von homogenem Verbundholz erfolgt gleichermaßen wie auf natürlichem Holz, ohne jegliche Eingrenzung und unter Beibehaltung der ästhetischen und funktionellen Eigenschaften des Produkts. Das Ergebnis ist kompakt und gleichmäßig, auch im Bereich des Schnitts. Ein koextrudiertes Produkt, das Bearbeitungen wie Längsschnitte oder Fräsen unterzogen wird, legt das Innenmaterial frei für Witterungseinflüsse, ohne jegliches Schutzschild, es wird also der weniger wertvolle Teil des Materials, der Kern, freigelegt, der nicht dazu gedacht ist, äußeren Einflüssen zu widerstehen. Das Produkt ist nicht dazu geeignet, mechanischen Bearbeitungen unterzogen zu werden, denn dies erzeugt einen mechanischen Schock zwischen Kern und Schutzfilm. Auch Kopfschnitte oder Schnitte, die zum Ablängen der Diele erforderlich sind, führen häufig zu Problemen mit der Ablösung des Schutzfilms.
Auch allgemeine Bearbeitungen von Profilen oder Tischlerarbeiten an Profilen wie "Wulst" und "Eulenschnabel" müssen berücksichtigt werden. Im Fall eine koextrudierten Produkts ist dies nicht möglich, da der "Kern" einer vorzeitigen Oxidation freigelegt würde. In allen Bereichen, in denen der Kern sichtbar ist, wird der empfindliche Teil des Produkts freigelegt und, wie schon gesagt, es bildet sich eine ungeschützte Zone der Struktur. Beide Produkte müssen mit geeigneten Werkzeugen bearbeitet werden, besser noch mit Sägeblättern Widia.
Fleckenanfälligkeit von WPC
Beide Produkte können Flüssigkeiten auf der Oberfläche absorbieren, die Flecken verursachen. Die Produkte aus homogener Masse mit den korrekten Zusatzstoffen werden nicht fleckig und besitzen eine gute Widerstandsfähigkeit gegen fremde Substanzen. Die Reinigung ist einfach und mit speziellen Produkten ist es möglich, fast jede Art von Flecken zu beseitigen. Ein koextrudiertes Material hat durch seinen äußeren Film aus Kunststoff eine geringere Absorptionsfähigkeit. Auch in diesem Fall ist es nötig, den Fleck schnellstmöglichst zu behandeln, um Schmutzränder zu vermeiden. Falls ein hartnäckiger Fleck auftritt, ist es auf jeden Fall möglich, das Produkt aus homogener Masse leicht zu schmirgeln, um diesen zu beseitigen. Aufgrund der homogenen Masse ist es möglich, diese Arbeit durchzuführen, ohne das Produkt zu beeinträchtigen. In einem koextrudierten Produkt ist dies nicht möglich, da der Film sehr dünn ist. Falls dort Flecken auftreten, ist die einzige Lösung der Austausch der betreffenden Diele. SIEHE BLOG REINIGUNG VON VERBUNDHOLZ
Schrammen auf der Oberfläche
Hinsichtlich der Gefahr von möglichen Schrammen oder Kratzern, besitzt das homogene Produkt deutliche Vorteile: es kann mit mittelgrobem Schleifpapier geschmirgelt werden, um diese zu beseitigen. Das koextrudierte Produkt hingegen kann im Fall von Schrammen nicht wieder hergestellt, sondern muss ausgetauscht werden.
Wiederverwertbarkeit von Verbundholz und Circular Economy
Ein außerordentlich wichtiges und aktuelles Thema ist die Wiederverwertbarkeit des Produkts. Nur einige Produkte aus homogener Masse können wieder verwertet werden. Die Produktionsunternehmen, die Studien über die Formulierung der Masse durchgeführt haben und die es ermöglicht haben, schon nach der ersten Extrusion das Produkt wieder zu verwerten, können am Ende seiner Lebensdauer kontaktiert werden, um das Recycling durchzuführen. Das Verfahren, das 2005 von Novowood als erstem Unternehmen vorgestellt wurde, hat es einer Reihe von Herstellern ermöglicht, sich an diese Vision anzupassen, und ist inzwischen zu einem begehrten ökologischen Meilenstein geworden. Der Prozess führt zum Beitritt in die so genannte Kette der Circular Economy, in der sowohl Hersteller als auch Verbraucher einbezogen werden. Dieser Vorgang erlaubt also die Ausnutzung der Ressourcen unseres Planeten zu reduzieren und sie durch das Recycling zu schonen.
Diese Regenerierung ist nicht möglich mit homogenen Produkten, die nicht von Anfang an für die Wiederverwertung entwickelt worden sind und auch nicht mit koextrudiertem Material, da dieses aus mindestens 2 verschiedenen Elementen besteht, der Kunststoff-Außenabschirmung und dem Kern. Natürlich ist dieser Prozess nur mit Produkten der ersten Generation möglich, die in Italien produziert wurden: Importierte Produkte besitzen auf nationalem Gebiet keine Unternehmen, die das Material zurücknehmen und können deswegen nicht recycelt werden.
Einige Händler von koextrudiertem Verbundholz, gerade um die Probleme der Wiederverwertbarkeit des Produkts zu verringern, berichten sie über eine Extrudierung mit zersetzbaren Kunststoffen. Offensichtlich gibt es kein Polymer, das in Holzverbundwerkstoffe eingefügt werden kann, das biokompatibel ist... wenn dies der Fall wäre, wäre das verkaufte Material sogar während seines Lebenszyklus "biokompatibel", was für den Endverbraucher eindeutig nicht von Vorteil ist.
Angesichts dieser Tatsachen haben viele Unternehmen, trotz der Marktentwicklung und des ständigen Anstiegs der Rohstoffpreise, die Produktion von extrudierten Produkten mit homogener Masse der ersten Generation aufrechterhalten, während viele andere, die mit neuen Technologien im Zusammenhang mit der Koextrusion von Holzverbundwerkstoffen experimentiert haben, im Laufe der Zeit einen Rückzieher gemacht haben, da es schwierig ist, ein Produkt herzustellen, das über einen längeren Zeitraum hinweg stabil ist und das tatsächlich eine Garantie für die Haltbarkeit ohne Probleme im Zusammenhang mit dem Schutzfilm gewährt.
In Italien hat sich kein Hersteller von Verbundholz dazu entschieden, seine Produktion umzustellen, um koextrudierte Materialien zu erhalten.
Veröffentlicht am 12 November 2020
Die ästhetischen Eigenschaften:
Das Verbundholz mit homogener Masse fühlt sich warm an, die freiliegenden Holzfasern vermitteln die unmittelbare Anlehnung an natürliches Holz. Es besitzt ein gleichmäßiges Aussehen und wenn es von hoher Qualität ist, kann man den Duft von Holz wahrnehmen. Die ästhetischen Eigenschaften des Produkts mit homogener Masse werden auch bei koextrudierten Produkten angestrebt, indem Muster und Schattierungen auf der Oberfläche der Kunststofffolie erzeugt werden. Das Produkt fühlt sich in diesem Fall kalt an und besitzt eine glänzendere Oberfläche. Um den künstlichen Effekt zu reduzieren schleifen einige Hersteller die Oberfläche, doch reduziert sich so die Dicke des Films und es bilden sich unansehnliche Plastikfäden.
Die Schnitte und Verarbeitungen auf Verbundholz:
Die Bearbeitung von homogenem Verbundholz erfolgt gleichermaßen wie auf natürlichem Holz, ohne jegliche Eingrenzung und unter Beibehaltung der ästhetischen und funktionellen Eigenschaften des Produkts. Das Ergebnis ist kompakt und gleichmäßig, auch im Bereich des Schnitts. Ein koextrudiertes Produkt, das Bearbeitungen wie Längsschnitte oder Fräsen unterzogen wird, legt das Innenmaterial frei für Witterungseinflüsse, ohne jegliches Schutzschild, es wird also der weniger wertvolle Teil des Materials, der Kern, freigelegt, der nicht dazu gedacht ist, äußeren Einflüssen zu widerstehen. Das Produkt ist nicht dazu geeignet, mechanischen Bearbeitungen unterzogen zu werden, denn dies erzeugt einen mechanischen Schock zwischen Kern und Schutzfilm. Auch Kopfschnitte oder Schnitte, die zum Ablängen der Diele erforderlich sind, führen häufig zu Problemen mit der Ablösung des Schutzfilms.
Auch allgemeine Bearbeitungen von Profilen oder Tischlerarbeiten an Profilen wie "Wulst" und "Eulenschnabel" müssen berücksichtigt werden. Im Fall eine koextrudierten Produkts ist dies nicht möglich, da der "Kern" einer vorzeitigen Oxidation freigelegt würde. In allen Bereichen, in denen der Kern sichtbar ist, wird der empfindliche Teil des Produkts freigelegt und, wie schon gesagt, es bildet sich eine ungeschützte Zone der Struktur. Beide Produkte müssen mit geeigneten Werkzeugen bearbeitet werden, besser noch mit Sägeblättern Widia.
Fleckenanfälligkeit von WPC
Beide Produkte können Flüssigkeiten auf der Oberfläche absorbieren, die Flecken verursachen. Die Produkte aus homogener Masse mit den korrekten Zusatzstoffen werden nicht fleckig und besitzen eine gute Widerstandsfähigkeit gegen fremde Substanzen. Die Reinigung ist einfach und mit speziellen Produkten ist es möglich, fast jede Art von Flecken zu beseitigen. Ein koextrudiertes Material hat durch seinen äußeren Film aus Kunststoff eine geringere Absorptionsfähigkeit. Auch in diesem Fall ist es nötig, den Fleck schnellstmöglichst zu behandeln, um Schmutzränder zu vermeiden. Falls ein hartnäckiger Fleck auftritt, ist es auf jeden Fall möglich, das Produkt aus homogener Masse leicht zu schmirgeln, um diesen zu beseitigen. Aufgrund der homogenen Masse ist es möglich, diese Arbeit durchzuführen, ohne das Produkt zu beeinträchtigen. In einem koextrudierten Produkt ist dies nicht möglich, da der Film sehr dünn ist. Falls dort Flecken auftreten, ist die einzige Lösung der Austausch der betreffenden Diele. SIEHE BLOG REINIGUNG VON VERBUNDHOLZ
Schrammen auf der Oberfläche
Hinsichtlich der Gefahr von möglichen Schrammen oder Kratzern, besitzt das homogene Produkt deutliche Vorteile: es kann mit mittelgrobem Schleifpapier geschmirgelt werden, um diese zu beseitigen. Das koextrudierte Produkt hingegen kann im Fall von Schrammen nicht wieder hergestellt, sondern muss ausgetauscht werden.
Wiederverwertbarkeit von Verbundholz und Circular Economy
Ein außerordentlich wichtiges und aktuelles Thema ist die Wiederverwertbarkeit des Produkts. Nur einige Produkte aus homogener Masse können wieder verwertet werden. Die Produktionsunternehmen, die Studien über die Formulierung der Masse durchgeführt haben und die es ermöglicht haben, schon nach der ersten Extrusion das Produkt wieder zu verwerten, können am Ende seiner Lebensdauer kontaktiert werden, um das Recycling durchzuführen. Das Verfahren, das 2005 von Novowood als erstem Unternehmen vorgestellt wurde, hat es einer Reihe von Herstellern ermöglicht, sich an diese Vision anzupassen, und ist inzwischen zu einem begehrten ökologischen Meilenstein geworden. Der Prozess führt zum Beitritt in die so genannte Kette der Circular Economy, in der sowohl Hersteller als auch Verbraucher einbezogen werden. Dieser Vorgang erlaubt also die Ausnutzung der Ressourcen unseres Planeten zu reduzieren und sie durch das Recycling zu schonen.
Diese Regenerierung ist nicht möglich mit homogenen Produkten, die nicht von Anfang an für die Wiederverwertung entwickelt worden sind und auch nicht mit koextrudiertem Material, da dieses aus mindestens 2 verschiedenen Elementen besteht, der Kunststoff-Außenabschirmung und dem Kern. Natürlich ist dieser Prozess nur mit Produkten der ersten Generation möglich, die in Italien produziert wurden: Importierte Produkte besitzen auf nationalem Gebiet keine Unternehmen, die das Material zurücknehmen und können deswegen nicht recycelt werden.
Einige Händler von koextrudiertem Verbundholz, gerade um die Probleme der Wiederverwertbarkeit des Produkts zu verringern, berichten sie über eine Extrudierung mit zersetzbaren Kunststoffen. Offensichtlich gibt es kein Polymer, das in Holzverbundwerkstoffe eingefügt werden kann, das biokompatibel ist... wenn dies der Fall wäre, wäre das verkaufte Material sogar während seines Lebenszyklus "biokompatibel", was für den Endverbraucher eindeutig nicht von Vorteil ist.
Angesichts dieser Tatsachen haben viele Unternehmen, trotz der Marktentwicklung und des ständigen Anstiegs der Rohstoffpreise, die Produktion von extrudierten Produkten mit homogener Masse der ersten Generation aufrechterhalten, während viele andere, die mit neuen Technologien im Zusammenhang mit der Koextrusion von Holzverbundwerkstoffen experimentiert haben, im Laufe der Zeit einen Rückzieher gemacht haben, da es schwierig ist, ein Produkt herzustellen, das über einen längeren Zeitraum hinweg stabil ist und das tatsächlich eine Garantie für die Haltbarkeit ohne Probleme im Zusammenhang mit dem Schutzfilm gewährt.
In Italien hat sich kein Hersteller von Verbundholz dazu entschieden, seine Produktion umzustellen, um koextrudierte Materialien zu erhalten.
Das könnte Sie auch interessieren
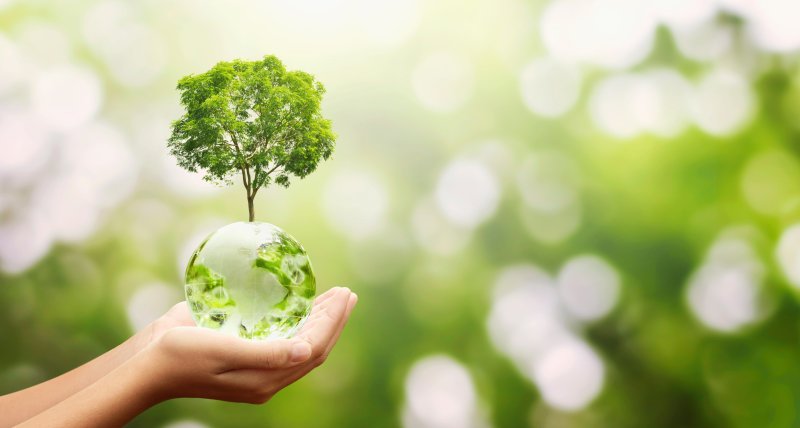
Der Respekt für die Umwelt ist der Respekt unser selbst.
Heute ist uns endlich bewusst, wie sich unser Verhalten auf die Umwelt auswirkt: Rohstoffeinsparungen und CO2-Emissionen sind zu Themen von allgemeine… Alles lesen
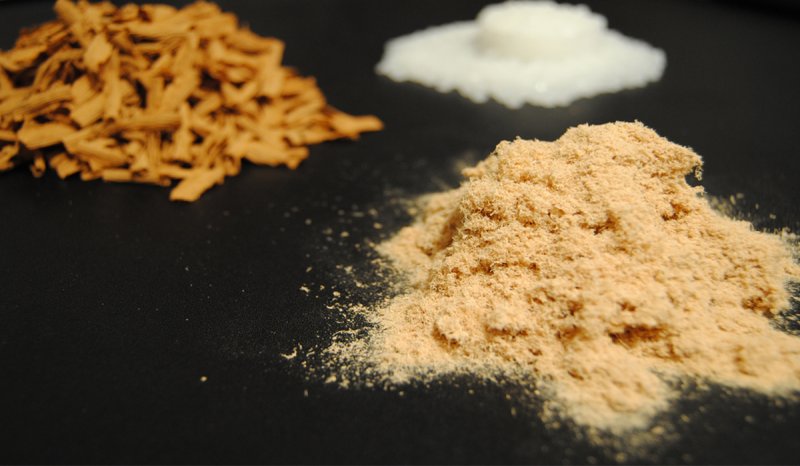
Was versteht man unter Verbundholz
Verbundholz ist ein Produkt, das als ökologischer Ersatz für Holz in Außenbereichen entwickelt wurde. Es wird auch als WPC bezeichnet,… Alles lesen
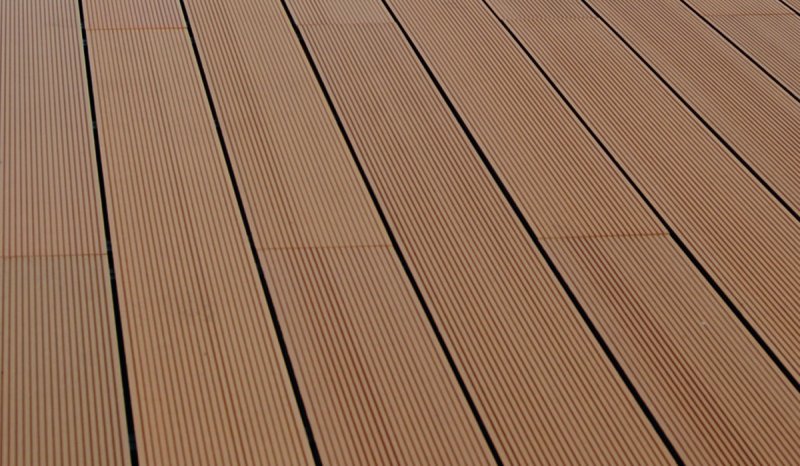
Die Wartung von Verbundholz
Das Verbundholz wurde hauptsächlich entwickelt, um die typische Wartung des Naturholzes zu vermeiden. Dadurch entfällt das für Holz typ… Alles lesen
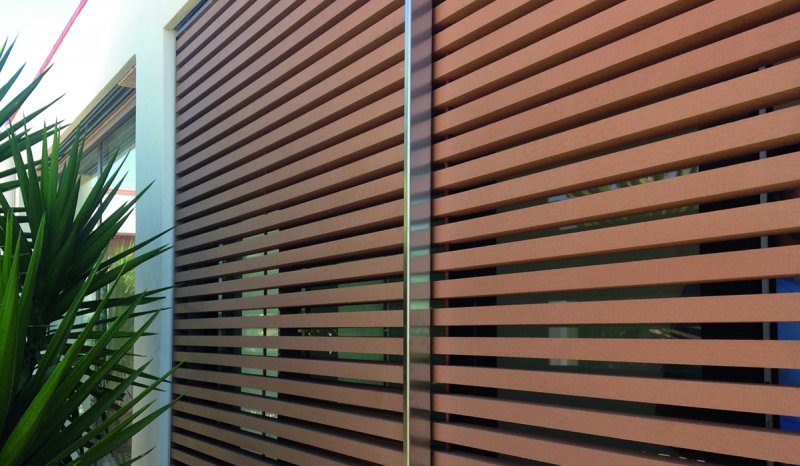
Sonnenschutz aus Verbundholz
Denken Sie an einen wunderschönen Sonnenschutz aus Holz. Bei der Montage bildschön, aber nach einigen Monaten beginnt er zu verbleichen. F&u… Alles lesen

Verbundholz Made in Italy
Made in Italy bestimmt die Produktionsherkunft des Materials. Das Made in Italy ist eine in der ganzen Welt geschätzte Eigenschaft. Weil: Made i… Alles lesen
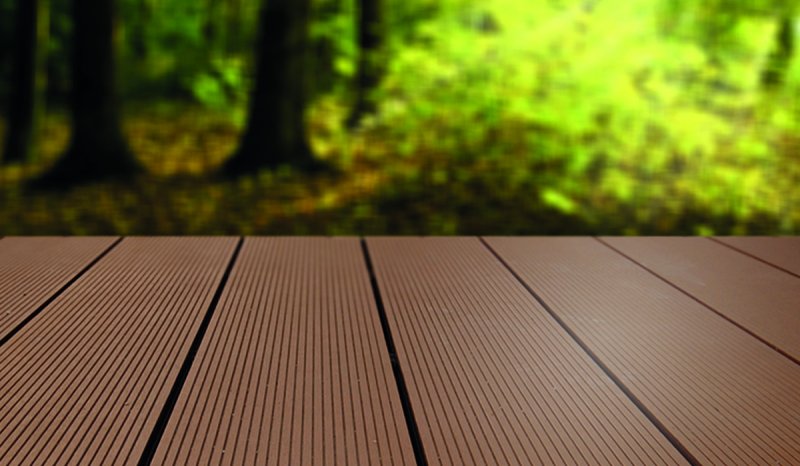
Preis von Verbundholz
Was ist der korrekte Preis für Verbundholz? Diese Frage stellen viele Internetnutzer, um zu verstehen, warum es auf dem Markt Preise gibt, die so… Alles lesen